The Role of CNC Machining in Precision Engineering
In today’s fast-paced industrial landscape, precision engineering is not just a desirable trait; it’s a non-negotiable standard. The seamless operation of heavy machinery hinges on the meticulous crafting of its components, demanding levels of accuracy and uniformity that only advanced manufacturing technologies can deliver. At the forefront of this technological revolution stands CNC machining, a sophisticated process that has reshaped the way we fabricate industrial parts, setting new benchmarks for precision and reliability.
CNC machining, short for Computer Numerical Control machining, represents a quantum leap in manufacturing capabilities. By harnessing the power of computer-controlled machinery, manufacturers can execute complex machining operations with unparalleled precision and efficiency. The process begins with a digital model of the desired component, which is then translated into machine-readable code. This code serves as a set of instructions for the CNC machine, guiding its movements with microscopic accuracy as it shapes raw materials into finished parts.
The Essence of CNC Machining: Precision, Efficiency, and Consistency
CNC machining stands as a testament to the relentless pursuit of precision in engineering. By leveraging advanced computer-controlled systems, CNC machines execute machining operations with unparalleled accuracy and consistency, ushering in a new era of manufacturing excellence. At its core, CNC machining is guided by digital models of the desired components, meticulously translated into machine-readable code that orchestrates every movement of the cutting tools.
One of the most compelling advantages of CNC machining is its ability to ensure consistency across large production runs. Unlike traditional machining methods, which rely heavily on manual intervention and are susceptible to human error, CNC machining operates with unfailing precision, producing components that adhere rigorously to predefined specifications. This uniformity is indispensable in industries where even the slightest deviation can spell disaster, such as aerospace engineering and medical device manufacturing.
Furthermore, CNC machining empowers manufacturers to push the boundaries of design innovation, unlocking new realms of possibility for engineers and designers. With advanced multi-axis machining capabilities, CNC machines can sculpt intricate geometries and complex features with breathtaking precision, enabling the realization of even the most ambitious visions. From intricate turbine blades to intricately contoured molds, CNC machining empowers creativity and fuels progress in engineering.
Moreover, CNC machining offers significant advantages in terms of efficiency and cost-effectiveness. By automating repetitive machining tasks and minimizing material wastage, CNC machining streamlines the production process, reducing lead times and maximizing productivity. The digital nature of CNC programming also facilitates rapid iteration on designs, enabling manufacturers to respond swiftly to changing market demands and customer preferences.
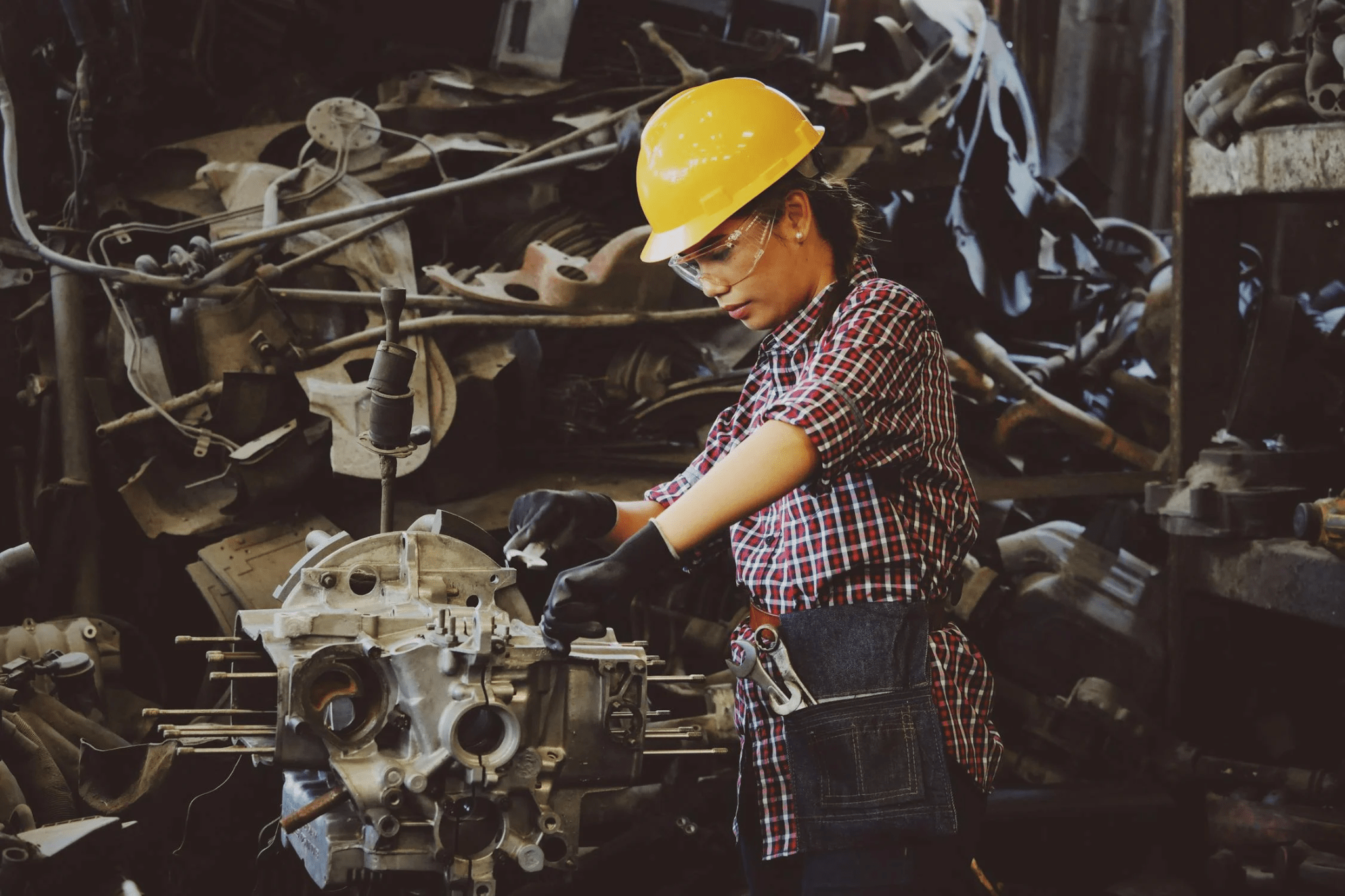
The Essence of CNC Machining: Precision, Efficiency, and Consistency
Delving deeper into the realm of CNC machining, we uncover its profound impact on the performance and reliability of industrial components. At the heart of CNC machining’s prowess lies its ability to ensure accurate sizing, tolerances, and surface finishes, key attributes that underpin the fitment and functionality of critical parts.
Accurate sizing is paramount in ensuring the proper functioning of mechanical systems, where even minor deviations can lead to catastrophic failure. CNC machining excels in this regard, delivering components with precise dimensions that meet the exacting requirements of engineering specifications. Whether it’s a precision bearing or a complex gear assembly, CNC machining ensures that every component fits seamlessly into its designated space, facilitating smooth operation and optimal performance.
In addition to precise sizing, CNC machining also guarantees tight tolerances, essential for maintaining the integrity and functionality of mechanical assemblies. Tolerances refer to the allowable deviation from a specified dimension, and in industries where precision is paramount, such as aerospace and automotive manufacturing, tight tolerances are non-negotiable. CNC machining excels in this regard, delivering components with ultra-precise tolerances that ensure perfect alignment and functionality.
Furthermore, CNC machining delivers impeccable surface finishes, a critical factor in reducing friction, wear, and corrosion in mechanical components. Whether it’s a mirror-like polish on a hydraulic piston or a precisely textured surface on a bearing race, CNC machining ensures that every component meets the highest standards of surface quality. This not only enhances the aesthetics of the final product but also prolongs its service life and reliability, ensuring years of trouble-free operation.
Conclusion:
In conclusion, CNC machining stands as a cornerstone of engineering excellence, revolutionizing the way we fabricate industrial components. Its ability to deliver unparalleled precision, consistency, and reliability has reshaped the manufacturing landscape, empowering engineers and manufacturers to push the boundaries of innovation. As industries continue to evolve and demand ever-higher levels of performance and reliability, CNC machining will undoubtedly remain at the forefront of technological advancement, driving progress and shaping the future of engineering excellence.
For those seeking to elevate their heavy machinery components to new heights of quality and reliability, Rock Tear Parts (RTP) offers a compelling solution. With a steadfast commitment to genuine OEM parts, innovation, and exceptional customer experience, RTP stands as a beacon of excellence in the industry. Partner with RTP today and experience firsthand the difference that precision engineering can make in your operations.